Introduction
The MIT Sustainable Engine Team (SET) doesn't just dream up innovative engine concepts; we build them. By taking pride in conducting 100% of fabrication in-house and on campus, we ensure rapid iteration, end-to-end optimization, and designs that are easy to make and therefore scalable. This empowers us to accelerate the journey from concept to reality, bringing our sustainable engine to the world faster.
Advanced Machining: Precision In-House
Engine components demand precision, and SET's in-house machining capabilities deliver:
- Simultaneous 5-axis machining: Complex turbine and impeller geometries take shape with optimal aerodynamic performance.
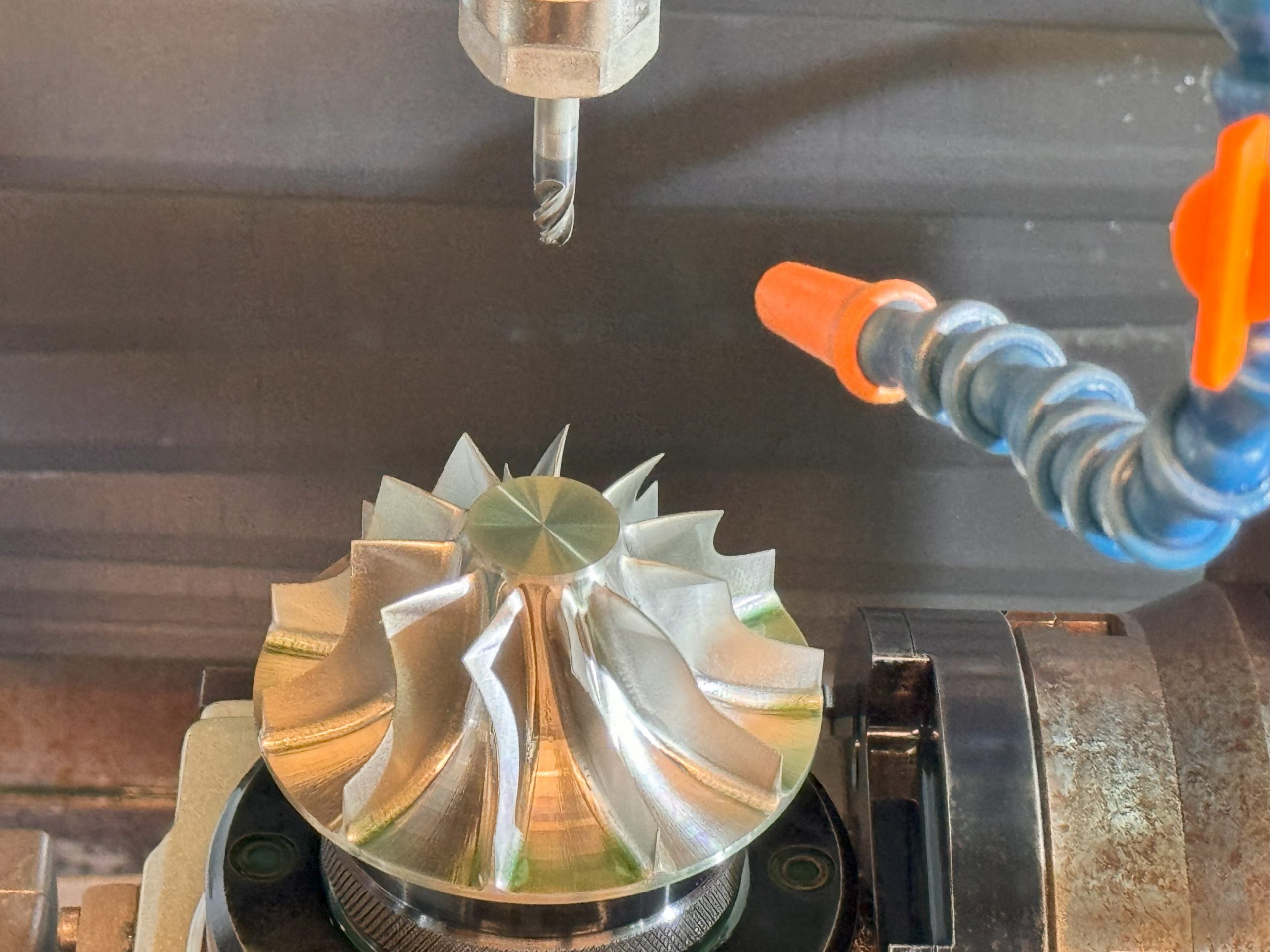
- Lathe: The crucial shroud, controlling engine airflow, is machined with precision.
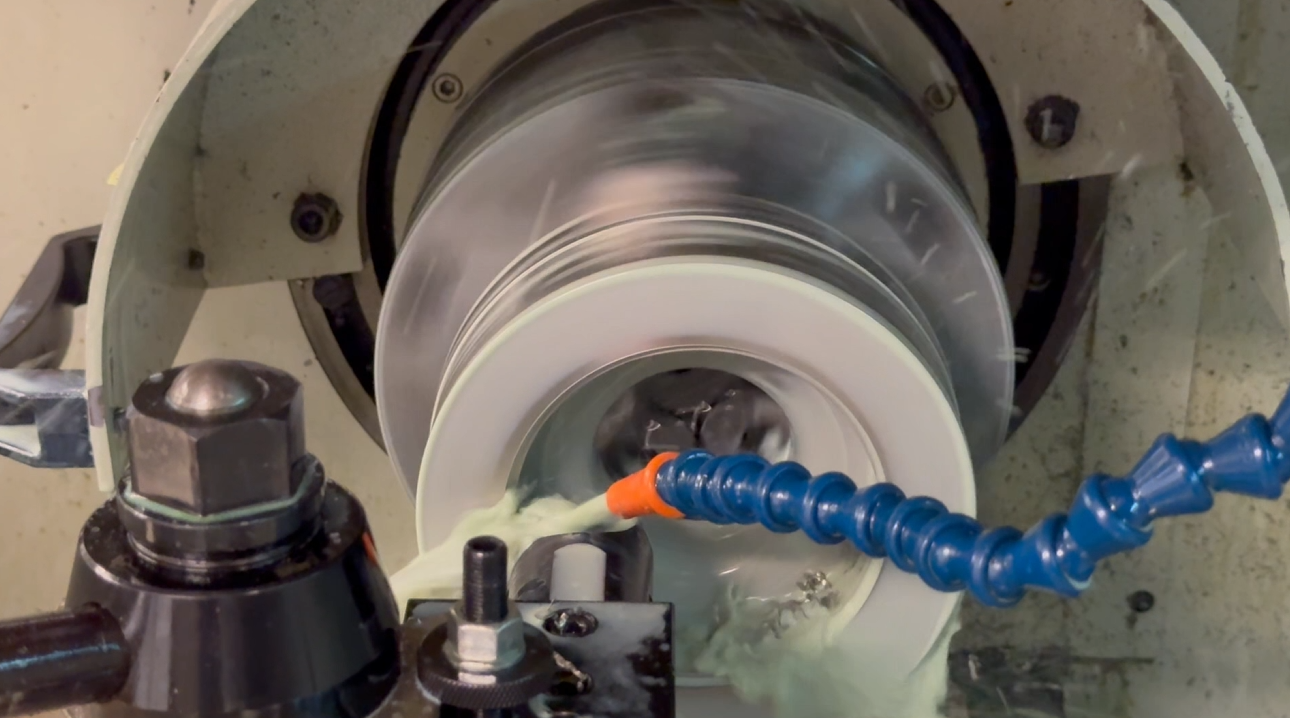
- Coordinate Measuring Machine (CMM): Every dimension is meticulously verified, ensuring each part meets exacting tolerances.
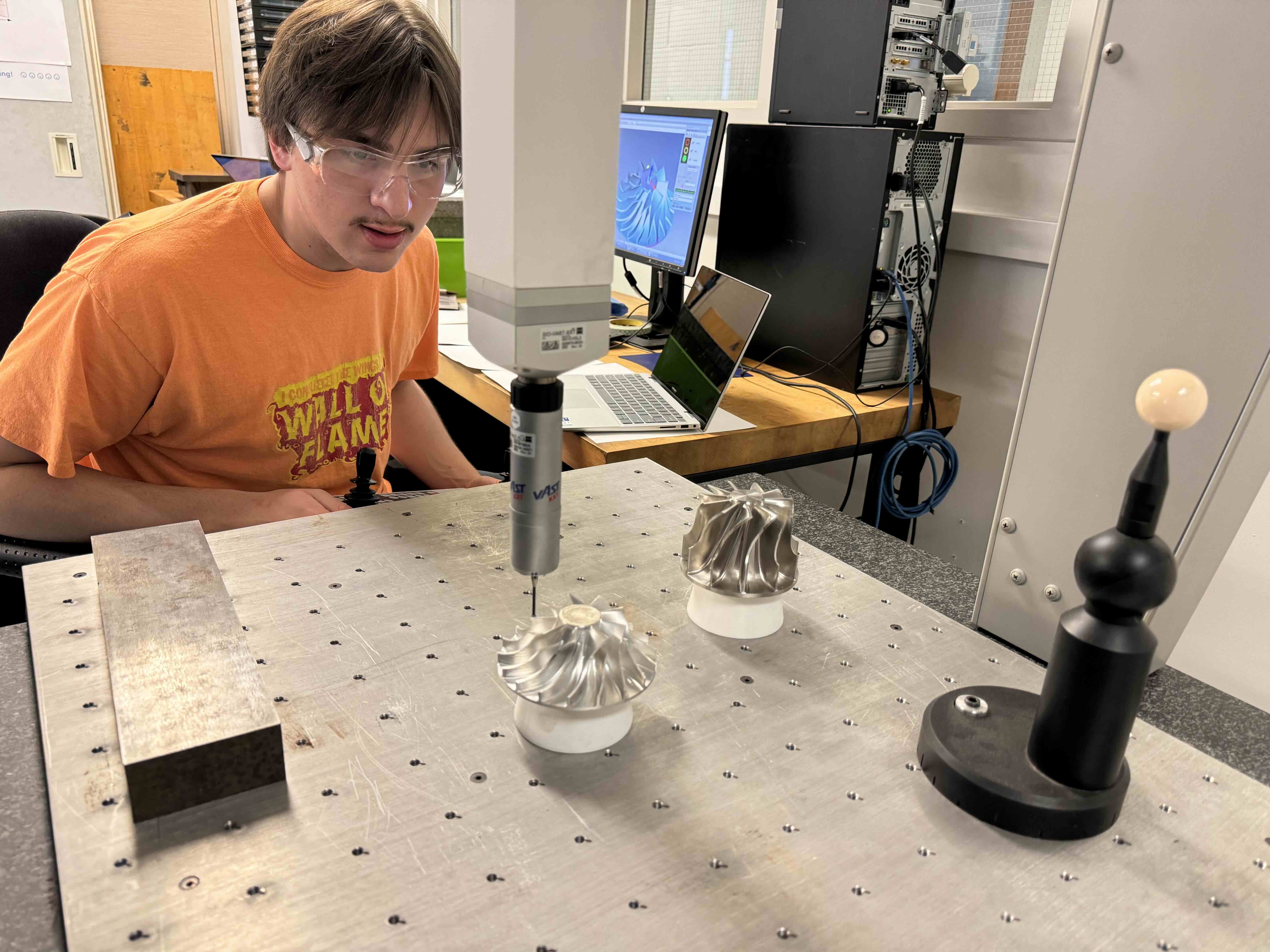
Sheet Metal Fabrication: Proven Processes for Rapid Prototyping
The engine's structure relies on precise sheet metal components, all fabricated on campus:
- Metal laser cutting: Complex shapes are cut with precision from sheet metal.
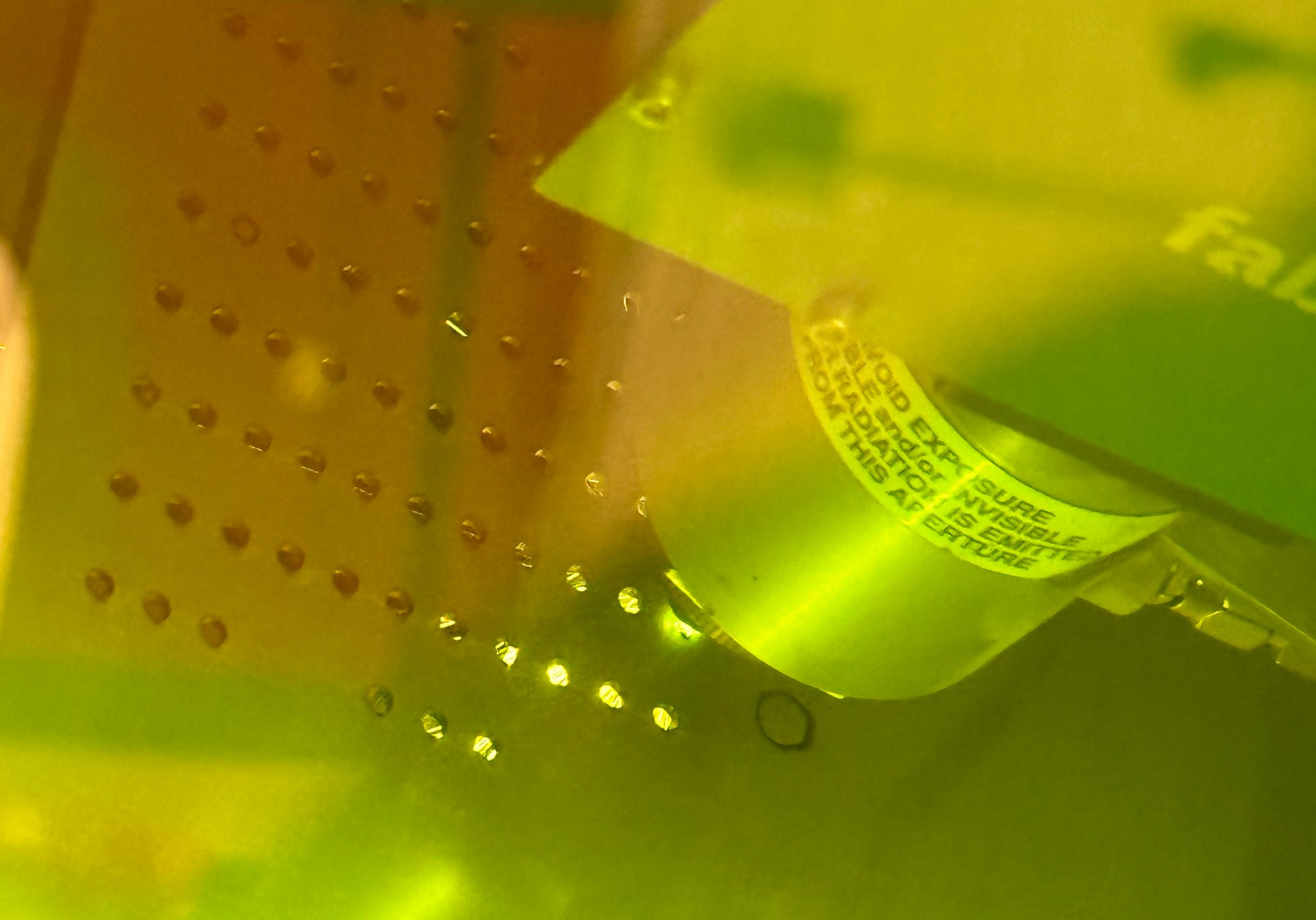
- Waterjet cutting: Thicker materials are handled with ease.
- TIG/MIG welding and Silver Brazing: Metal components are joined with strength.
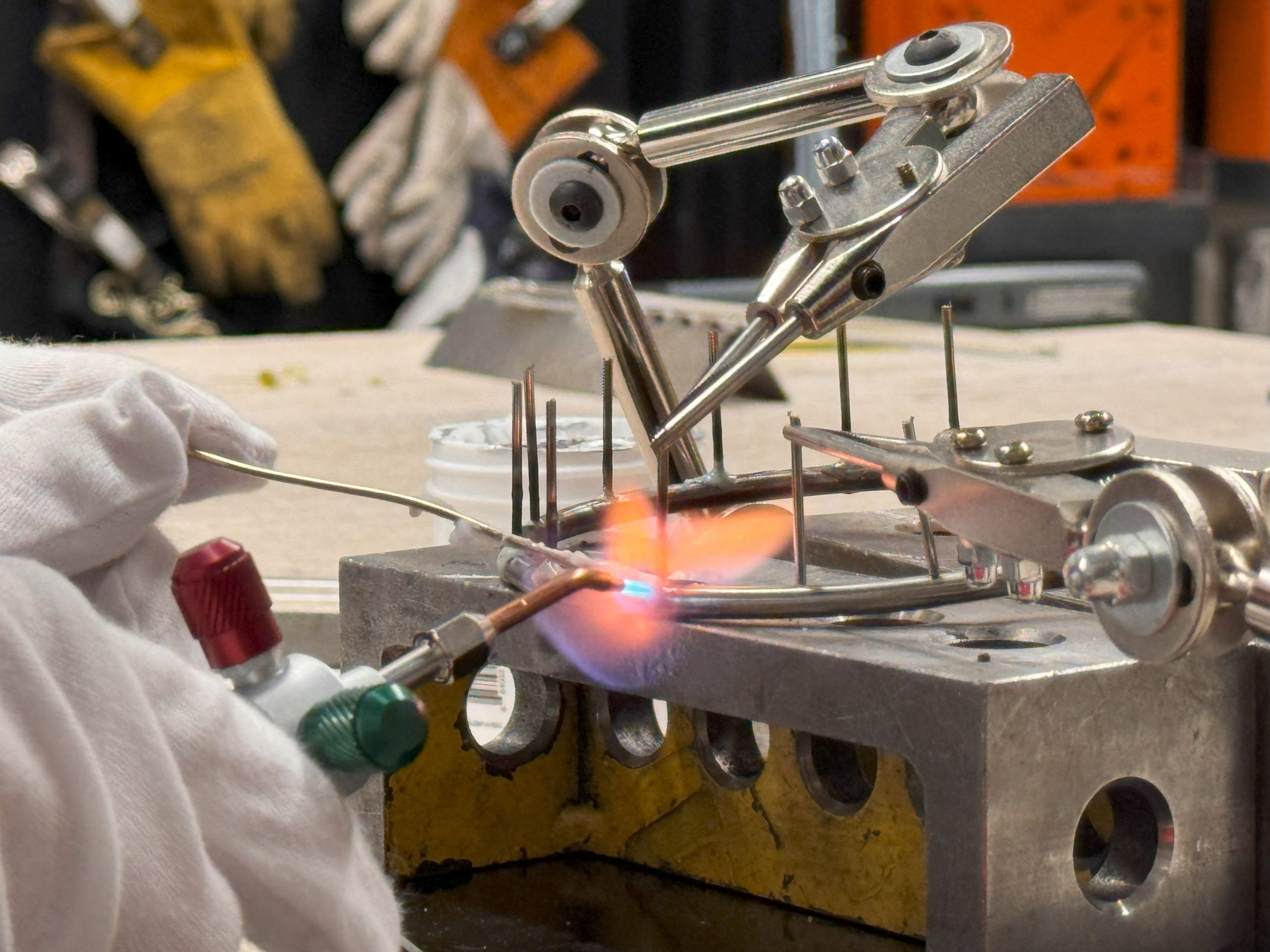
Advanced Materials: Performance-Driven Choices
We go beyond traditional materials, choosing the latest advancements for sustainability:
- Turbine: High-temperature, corrosion-resistant 316 SS and Inconel 718 tackle the turbine's harsh environment. For the 24-25 cycle, we are investigating the possibility of using Niobium alloy to dramatically boost efficiency.
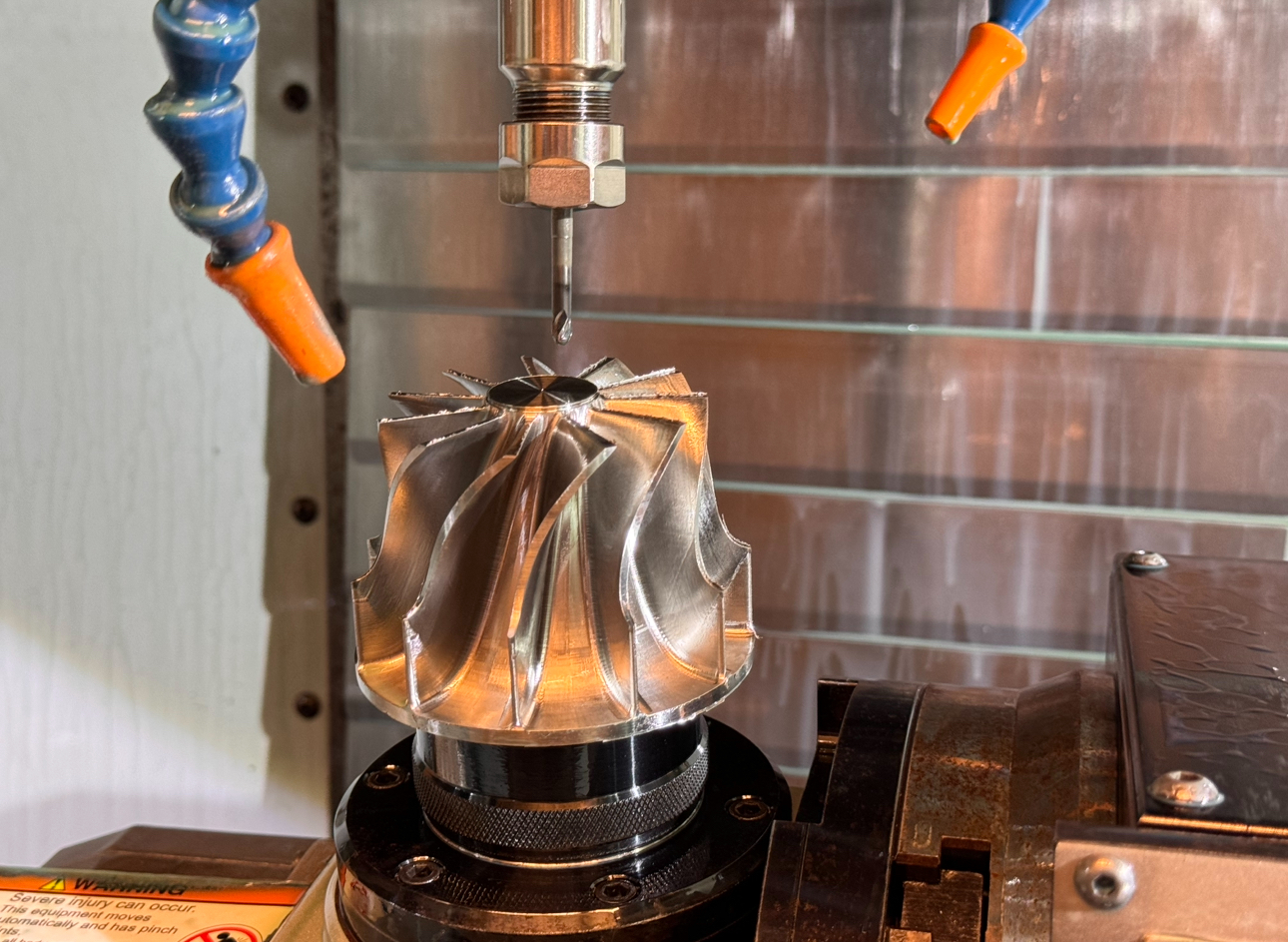
- Combustor: Incoloy 330, known for strength and oxidation resistance, is selected for the combustor's intense heat. For the 24-25 cycle, we are testing ceramic 3D printing for the combustor.
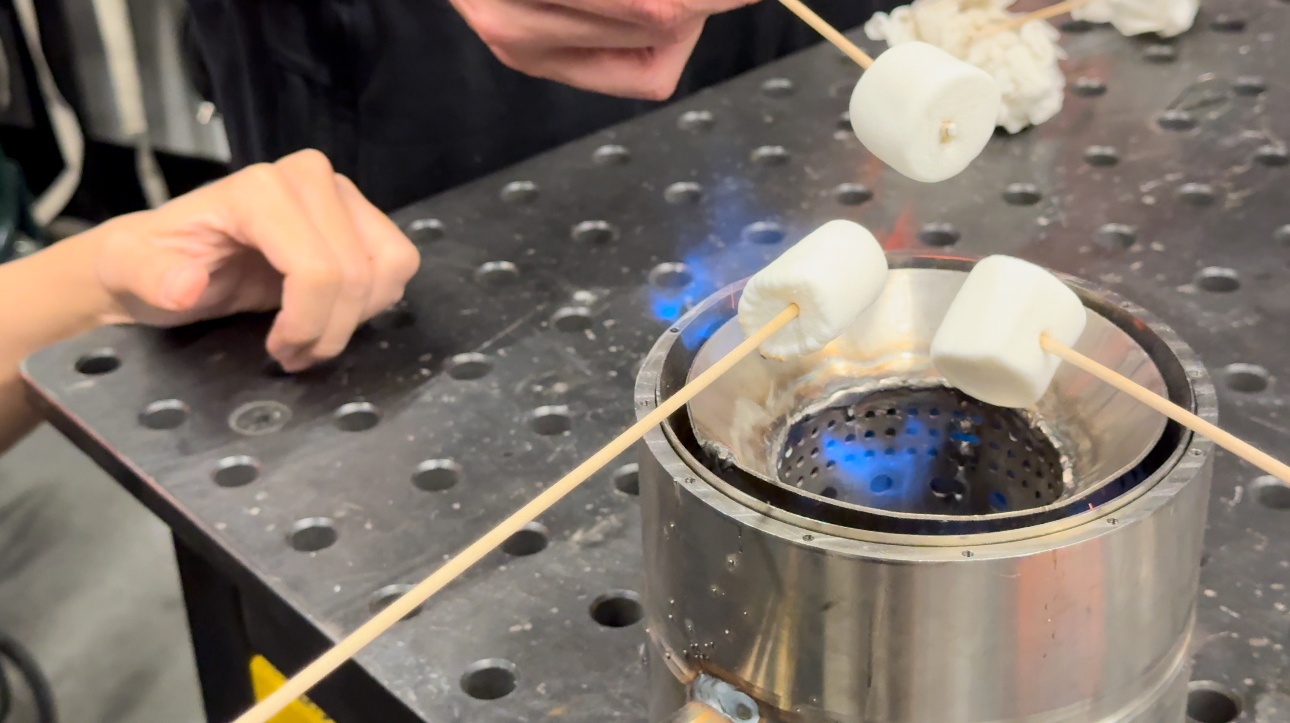
- Impeller: Lightweight and strong Ti-6Al-4V (titanium alloy) is perfect for the impeller's demanding role.
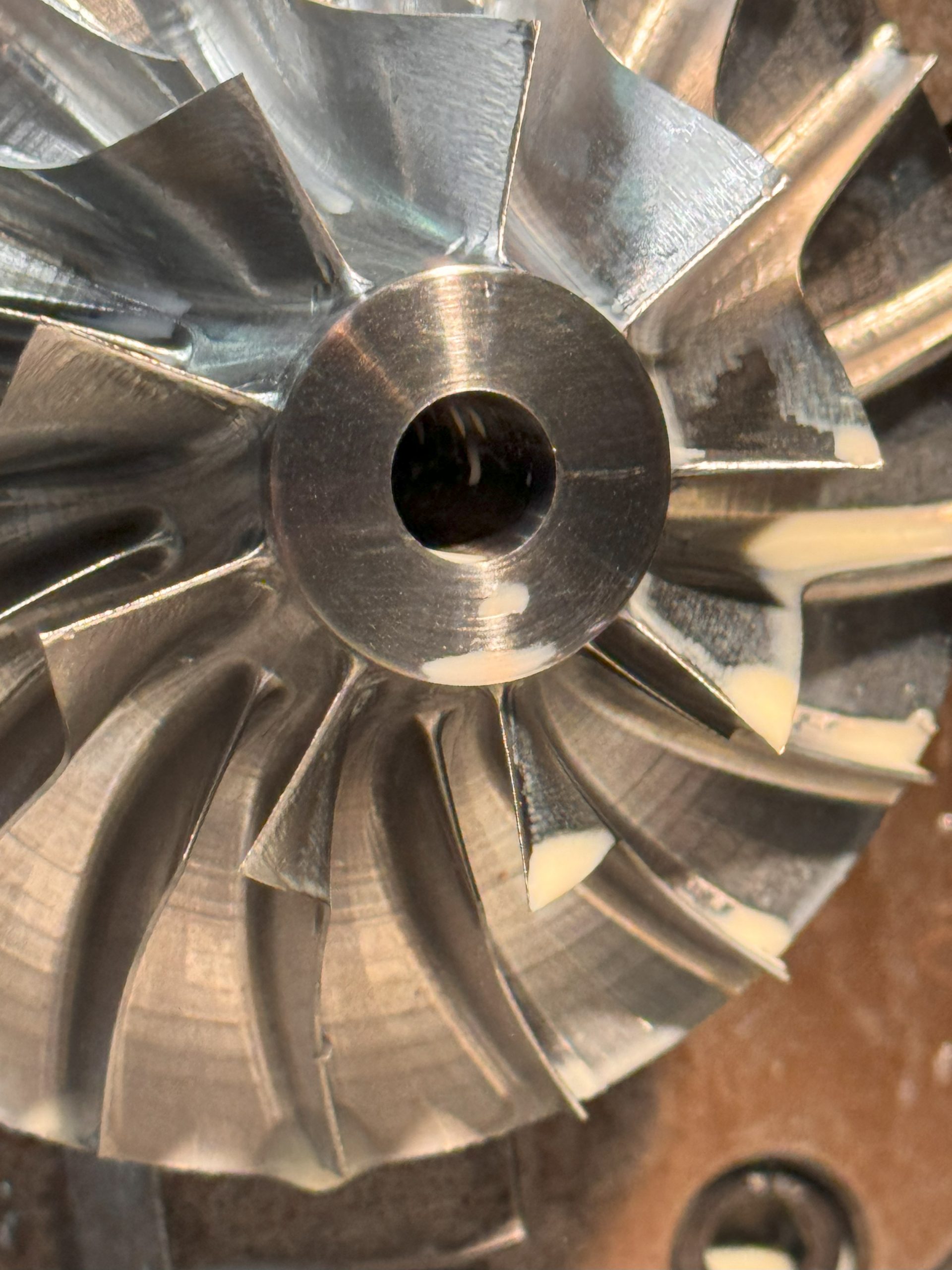
Conclusion
The MIT Sustainable Engine Team's dedication to in-house fabrication is a testament to our commitment to innovation and practicality. By leveraging MIT's resources and conducting 100% of fabrication on campus, we ensure rapid iteration and designs that are both manufacturable and scalable, speeding the path from concept to real-world impact. Our hands-on approach is paving the way for a future where sustainable engines are not just a vision but a reality.